Influencia del entorno y de las condiciones de la superficie
El acero se corroe porque es un producto humano, inestable porque por ejemplo el hierro, uno de sus principales componentes siempre tenderá a volver a su estado natural, óxido de hierro, propiciado por la corrosión.
Es más probable que tenga lugar la corrosión cuando están presentes uno o más de los siguientes factores:
- Humedad elevada, que proporciona el agua esencial; es decir, humedad superior al 60%.
- Contaminación atmosférica, que proporciona impurezas, por ejemplo, sulfuros y cloruros.
- La presencia de cascarilla de laminación con grietas o discontinuidades; la cascarilla o calamina mostrada en la Figura 1 se convierte en el polo positivo (cátodo) y el acero en el negativo (ánodo), disolviendo o corroyendo el polo (ánodo) en la célula de corrosión.
¿Proteger con qué?
El modo más práctico de proteger el acero es la aplicación de otra capa que actúe como ánodo (es decir, que se disuelva preferiblemente en acero), como barrera, o como ambas cosas. Los revestimientos más comunes son las pinturas, la galvanización por inmersión en caliente, el metalizado con cinc o aluminio, y cualquiera de los tres últimos revestidos con pintura.
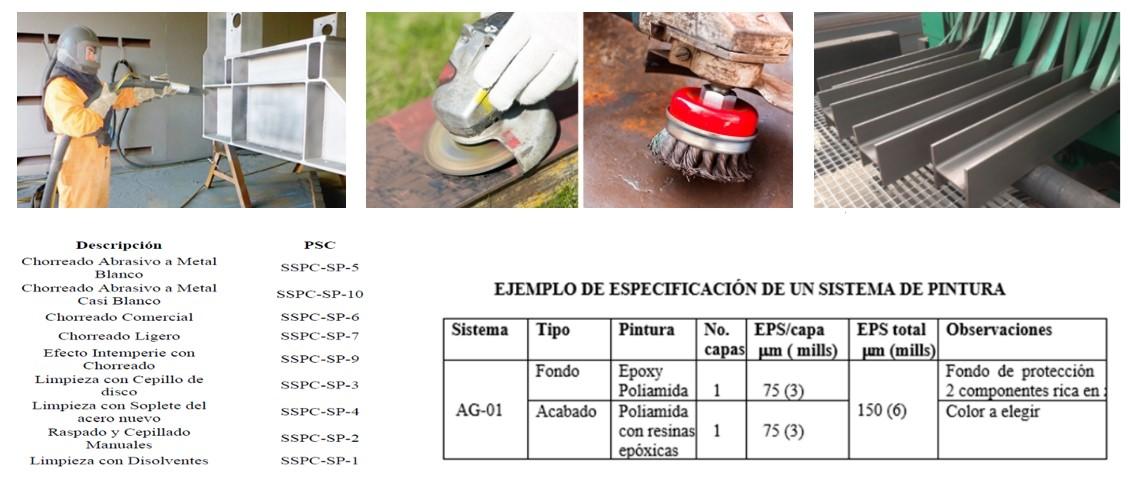
Fig. 2– Preparación de Superficies y Sistema de Pintura
Preparación de la superficie
La preparación de la superficie, tal y como se muestra en la Figura 2, ejerce una importante influencia en la determinación del valor protector de un sistema de revestimiento. En el caso de los revestimientos metálicos suele ser parte integral del proceso de fabricación y se incluye en las normas aplicables del caso. Con las pinturas, el tipo y modelo de preparación de la superficie debiera especificarse como parte del tratamiento de revestimiento de protección. La importancia de eliminar la cascarilla de laminación (calamina) ha quedado bien establecida. Los métodos empleados con este propósito son los siguientes:
- Picado, Rascado y cepillado con alambre
- Pistolas neumáticas descascarilladoras
- Decapado ácido
- Limpieza por chorro abrasivo
- La rugosidad superficial es importante en relación con el perfil obtenido por chorro abrasivo, que hace que la superficie del acero se haga rugosa (Figura 3).
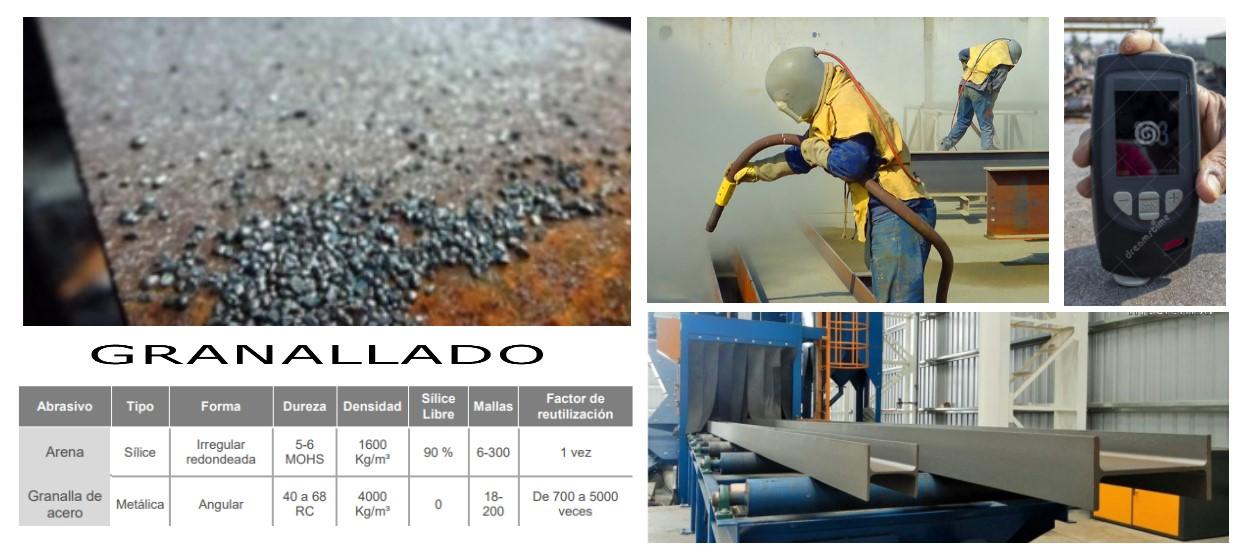
Fig. 3 – Limpieza por Chorro Abrasivo conocido por Granallado.
Antes de pintar se deberá eliminar la grasa, el aceite, el polvo y cualquier otro contaminante depositado sobre la superficie a tratar después de preparada. En el caso de que aparezcan zonas oxidadas después de haber preparado la superficie, éstas deberán ser nuevamente limpiadas. Es necesario siempre consultar con las tablas y sistemas establecidos por los fabricantes de pinturas y con la normativa del AMERICAN PAITING COUNCIL, APC.
Los trabajos de preparación de superficies están normalizados por varias asociaciones internacionales siendo una de la más difundidas la norma americana SSPC (Steel Structures Painting Council, Pittsburgh USA, Tabla 1) definiendo en cada categoría los distintos procedimientos requeridos para realizar una correcta limpieza de superficie de superficie previo a la aplicación de un revestimiento o pintura,
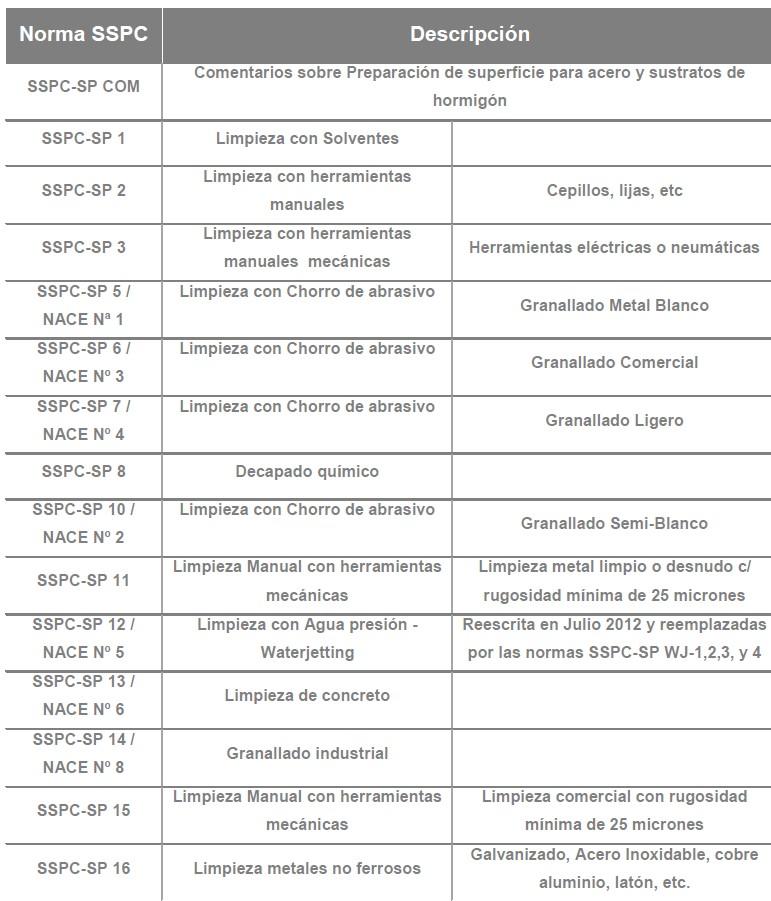
Tabla. 1 – Procedimientos según la norma americana SSPC.
Sistemas de pintado
Las pinturas tienen tres componentes principales: un componente resinoso que literalmente pega el resto de componentes y al que se denomina “formador de película” (film former); un pigmento encargado de dar color, resistencia a la corrosión atmosférica y, en algunos casos, una inhibición de la corrosión; y disolventes destinados a proporcionar la adecuada consistencia para la aplicación, control de la velocidad de secado, etc.
En un sistema de pintado suele haber tres componentes:
- Imprimación: Sus funciones son favorecer la adherencia y proteger contra la corrosión. Puesto que el espesor del sistema es muy importante para la protección, con frecuencia se especifican dos capas, y a veces tres cuando las dos últimas se aplican con brocha.
- Capa intermedia (undercoat): En el acero las capas intermedias tradicionales proporcionan la base de color adecuada para el acabado; se adhieren a la imprimación, y poco más. La capa intermedia de alto rendimiento se describe con más precisión en inglés como “Intermediate coat”. Constituye una segunda barrera en caso de que el acero quedara al descubierto por daños o erosión. A menudo las capas que se utilizan con este fin pueden pasar, por sí mismas, como acabados. Un aspecto importante es obtener un espesor de película seca. Una capa intermedia tradicional ofrece alrededor de 25 µm por capa; las utilizadas en el acero en entornos no naturales deben ofrecer un espesor mínimo de 50 µm, mientras que los tipos de alto rendimiento de servicio producen 100 µm o más.
- Acabado: Proporcionan el color, nivel de brillo o resplandor requeridos y la conveniente resistencia a la corrosión atmosférica, a la abrasión o al ataque químico. Puede ser necesaria más de una capa dependiendo del tipo de producto, de la exposición, del entorno, del color, etc. Los espesores de película seca por capa varían, de 25 mm para un producto simple aceitoso, a 100 mm o más para revestimientos epóxicos de dos envases.
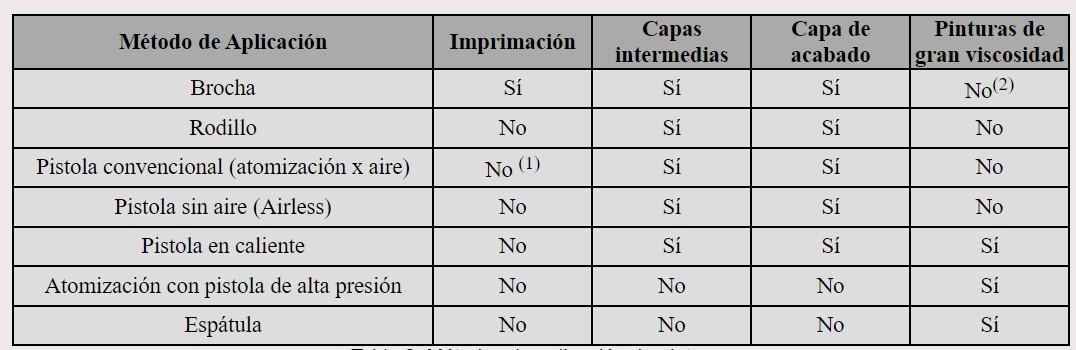
Tabla. 2 – Métodos de aplicación de pinturas.
Galvanización por inmersión en caliente
El galvanizado consiste en la inmersión de piezas de acero en zinc fundido para protegerlas de la corrosión y potenciar su fortaleza mecánica a los golpes y a la abrasión. El proceso es inherentemente simple, lo que brinda una ventaja distintiva en contraste con otros métodos de protección contra la corrosión.
La preparación de la superficie para el galvanizado consta de tres pasos definidos como: Desengrasado, Decapado y Aplicación de flujos con una solución de cloruro de amonio de zinc, para eliminar cualquier óxido restante y deposita una capa protectora en el acero para impedir que se formen más óxidos en la superficie antes de la inmersión en el zinc fundido.
En la verdadera instancia de galvanizado del proceso, se sumerge por completo el material en un baño de zinc fundido. La química del baño está especificada según el ASTM, y requiere al menos 98% de zinc puro mantenido a aproximadamente 449 ºC (840 ºF) hasta lograr un recubrimiento de al menos 7-42 micras. Mientras está sumergido en la caldera, el zinc reacciona con el hierro en el acero y forma una serie de capas intermetálicas de aleación zinc/hierro. Una vez que se completa el crecimiento del revestimiento de los artículos fabricados, se los puede retirar del baño de galvanizado, y se elimina el exceso de zinc mediante drenaje, vibración y/o centrifugado.
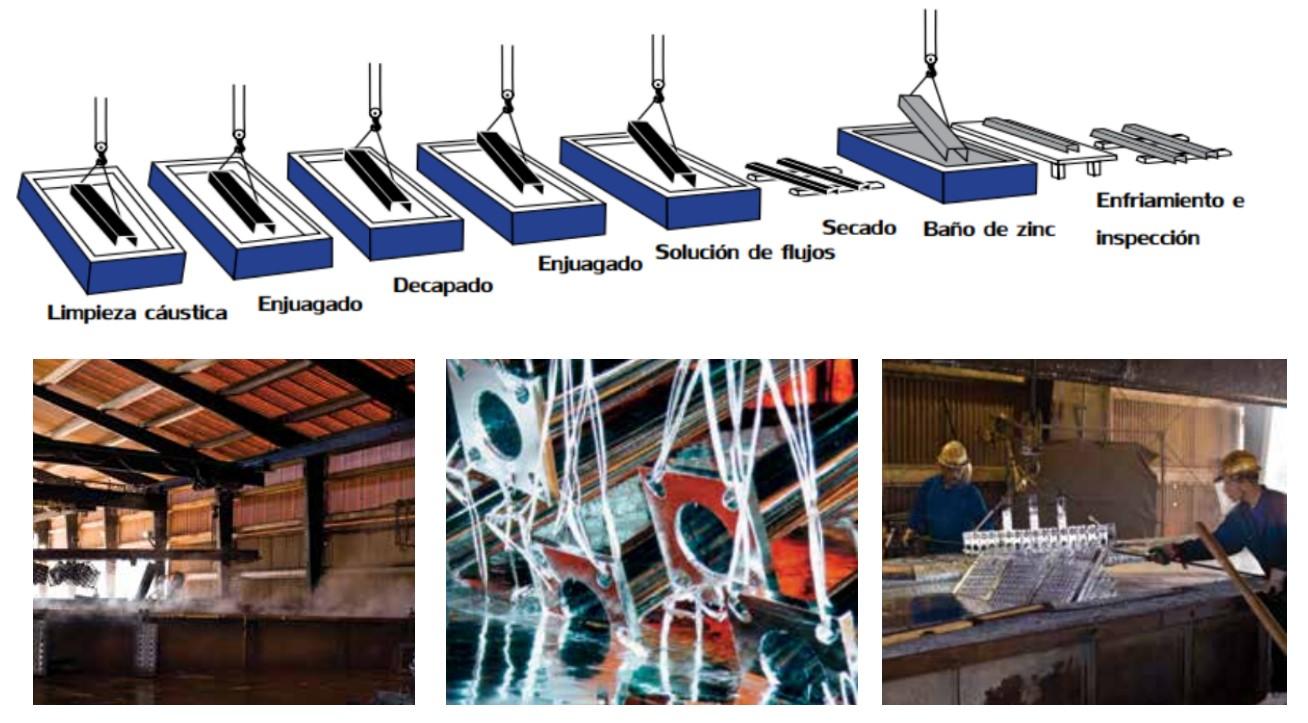
Fig. 4 – Proceso de Galvanizado en Caliente.